Robotics in general and particularly Cobots have a strong impact within highly automated production facilities. As market demands transformation and demographic change induce new challenges on mass production, CONTI has already undergone feasibility and profitability assessment for the application of flexible Cobots in upcoming assembly facilities. In parallel, CONTI investigates Cobots and AGVs with respect to the strict requirements of electronic production and has gained deep insight into industrial needs and problem settings. The leadplant of CONTI for advanced driver assistance systems (BU ADAS) is located in Ingolstadt. The plant has a high level of automation in production and logistics as well as high specialization in cobots and AGVs. Innovative manufacturing processes are set up in Ingolstadt for the first time and upon successful verification are transferred to the other ADAS sites.
Smart Manufacturing & Industry 4.0 Use Cases & Living Lab
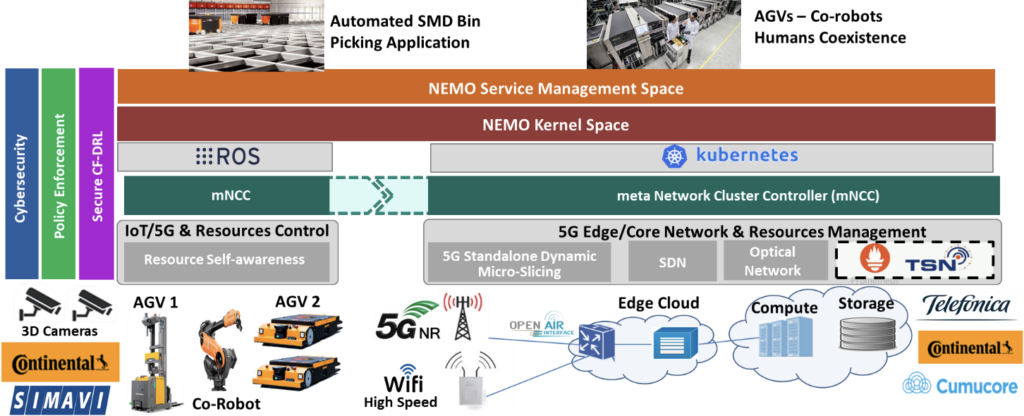
Use case Applications
- Fully automated indoor logistics/supply chain: This use case targets ADAS manufacturing. Today, handling and transport of material (SMD-Components) from Auto Store to production sites is performed manually every 30 minutes. By utilizing a 3D-Vision-Camera for Bin Picking Application, integrated Barcode Scanner and collaboration between different robot systems (one cobot and several types of AGVs), we aim to fully automate controlled material picking from Auto Store and autonomous transfer to the production line.
- Human-centred indoor factory environment safety. This use case will provide a high precision AGV localization layer merging real time localizations info obtained from cognitive sensors (safety cameras, radar and lidar). A high speed and ultra-low latency (TSN) private wireless network will support massive data uploads to the edge cloud facilities, where AI functions will detect the position of each body and build a “safety shell” around it to ensure human-centred safety, while federated CF-DRL will enable model transfer learning to the AGVs to enable autonomous avoidance of potential collision between AGVs, or between a worker and an AGV.
NEMO as Industry 4.0 & Smart indoor Logistics/Supply Chain Differentiator
- Combine 3D Vision, heterogeneous networks, edge (remote) and semi-autonomous (on-device) CF-DRL/ Transfer Learning, enabling fully automated SMD-Components recognition and transfer to production site
- AGVs-AGVs and AGVs-humans collision prediction, detection and avoidance through real-time cm-level High Accuracy Indoor Positioning (HAIP) and CF-DRL functions hosted locally on the IoT nodes and in 5G edge.
- Digital powertrain optimization (production, process, asset and energy) in brown field factories
- Validate NEMO user acceptance from an industry employee viewpoint by validating efficiency and productivity